VRM Services
Meer dan 30 jaar ervaring in technische ondersteuning van internationale industrieële klanten, van storing zoeken tot en met het begeleiden van complexe installaties als Site Supervisor.
Door de brede ervaring met verschillende technische disciplines is inzet op korte termijn vaak geen probleem.
Expertise
International Field Service
International Site Supervisor
Oil & Gas industry
Food Processing
Poultry Processing
Infant Nutricion
Logistic Automation
High Tech Semi conductor Industry
3D desing & printing
Machine veiligheid support
CE Markering support
Werkwijze
We werken met klant specifieke contracten waarbij we kijken wat het beste aansluit bij de bestaande inleen cultuur van de desbetreffende opdrachtgever. De ene keer is dat een jaarcontract, de andere keer een opdracht voor een specifiek
project.
Vooraf bepalen we samen met de klant wat de scope is van het werk en welke kosten hierbij komen kijken.
Field Service met een hoofdletter S
Bij VRM Services begrijpen we dat Field Services niet zomaar een taak is, maar een cruciaal element in het succes van elk bedrijf. Met trots presenteren we onze toonaangevende diensten op het gebied van Field Services, waarbij de ‘S’ in Services altijd met een hoofdletter wordt geschreven.
International ervaring
Het is niet voor iedereen weggelegd om internationaal te opereren. Niet alleen heb je te maken met het project op zich, ook het reizen en van huis zijn kan een uitdaging zijn. Verder heb je vaak te maken met andere culturen en gewoonten, is de omgeving niet altijd wat je gewend bent, zijn faciliteiten niet vanzelfsprekend, werk je onder zwaardere klimatologische omstandigheden en kan een taalbarière tot miscommunicatie leiden.
Communicatie
Als je de communicatie op orde hebt scheelt dit vaak al een hoop onduidelijkheid. Communicatie betreft niet alleen het informeren van de opdrachtgever over de voortgang van het project, ook ter plaatse zal met de klant overleg gepleegd moeten worden en zal met andere partijen (subcontractors en derde partijen) informatie moeten worden uitgewisseld om fouten en misverstanden te voorkomen.
Communiceren kan zowel schriftelijk als mondeling in 4 moderne talen Nederlands, Engels, Duits en Frans.
Rapportages
We zijn gewend om de voortgang van projecten regelmatig en duidelijk te communiceren met alle betrokken partijen. Vaak gebeurd dit in de Engelse taal vanwege het internationale karakter. Met eigen templates en software kunnen we punchlists genereren en deze distribueren onder de betrokken partijen. Veelal word ook gebruik gemaakt van software en templates die de opdrachtgever als standaard gebruikt.
Kortom VRM Services past zich als flexibele partner aan de bedrijfscultuur van haar opdrachtgevers aan, en waar mogelijk probeert ze haar steentje bij te dragen aan proffesionalisering van rapportages en communicatie.
Oplossingen
Regelmatig lopen we tijdens projecten tegen problemen aan welke niet altijd op voorhand voorkomen hadden kunnen worden. Soms blijkt de praktijk niet overeen te komen met het design of blijken de omstandigheden anders dan verwacht.
Vanuit ervaring met allerlei projecten en diversiteit van industrieën kunnen we regelmatig met een slimme oplossing of aanpassing het probleem tackelen zonder dat daar kostbare en/of ingrijpende aanpassingen voor nodig zijn.
In eigen beheer kunnen we in 3D componenten ontwerpen welke we vervolgens op hoogwaardige industrieële 3D printers produceren.
Projecten en opdrachtgevers
Logistic Automation projects
Amazon Fullfilment & Sortcenters
Opdrachtgever Vanderlande Industries B.V.
Commissioning Supervisor
Op de eerste projecten voor Vanderlande GmbH in Duitsland en Polen werd ik ingezet als Commissioning Supervisor. Samen met een lokaal team controle uitvoeren zodat uiteindelijk het equipment geinstalleerd door de contractor volgens specificatie was gebouwd, veilig en operationeel was om de Commissioning fase zonder problemen door te komen. Daarbij hoorde ook de overdracht van equipment naar de eindgebruiker Amazon
Lead Supervisor
Vanwege mijn ervaring met ondertussen vele Amazon projecten groeide ik verder door naar Lead Supervisor voor zowel electrische als mechanische uitdagingen. Het out-of-the-box denken en flexibele instelling zorgde ervoor dat verschillende lastige problemen in kort tijdsbestek opgelost konden worden.
Ondermeer door zelfbedachte oplossingen ook in eigen beheer te produceren (3D Printing) en vervolgens on-site te testen en te implementeren.
Poultry Processing plants
Lincoln Premium Poultry
Opdrachtgever Marel B.V.
Site Construction Supervisor
Op dit prestige project in Nebraska USA de eerste machines en lijnen geinstalleerd voor de delenlijnen met een capaciteit tot wel 8.400 bph (140 bpm). Naast dit project verschillende andere nieuwbouw installaties mogen voltooien, onder meer een van de grootste plants van Harim waar we 4 productielijnen over 5 verschillende verdiepingen hebben geinstalleerd.
Oil and Gas Industry
Inert Gas Systems and Exhaust Gas Cleaning
Opdrachtgever Alfa Laval Nijmegen B.V.
Field Service & Commissioning Engineer
Jarenlange ervaring als Field Service & Commissioning Engineer voor Alfa Laval Inert Gas Systemen.
Verschillende type systemen zoals de standaard generatoren, membraansystemen en Exhaust Gas Scrubbers
Expertises
Mechatronische competenties dus zowel mechanisch, electrisch alsook PLC kennis.
Ondersteuning bij het in de markt zetten van proto type oplossingen zoals EGC (Exhaust Gas Cleaning) , AFEM (Automatic Fuel Efficiency Module).
E-learning and Maintenance programma’s.
Food Processing Industry
Fully automated Lollypop processing and coating line
Opdrachtgever GEA Aquarius B.V.
Field Service & Commissioning Engineer
Nadat ik diverse sugar cube machines mocht installeren en reviseren voor GEA Aquarius in met name Afrikaanse landen heb ik samen met een vaste medewerker in Mexico een volledig geautomatiseerde productielijn geinstalleerd en gecommissioned. Hier werden lolly’s gevormd welke vervolgens werden voorzien van een chilipeper coating en aan het einde van de lijn verpakt op een transportsysteem werden gedeponeert.
Food Processing Industry
Baby Nutricion production plant
Opdrachtgever Mead Johnson Nijmegen B.V.
Site Construction Coördinator
Ter ondersteuning van het Engineerings team heb ik gedurende een aantal maanden bij grote ombouw, nieuwbouw en onderhoudsprojecten aansturing gegeven aan de betrokken contractors. Hierbij zijn intern diverse ruimten onder handen genomen en extern de waterzuivering compleet gereviseerd alsmede een nieuw gebouw voor de CIP installatie gerealiseerd.
Power Industry
Electrical Power Plant DGEN India
Opdrachtgever Petrogas B.V.
Site Construction Coördinator
In samenwerking met het lokale team van Siemens en contractors het Fuel Gas treatment systeem afgebouwd en gereed gemaakt voor de commissioning. Een bijzonder project waar dagelijks zo’n 5.000 contractors werkzaamheden uitvoerden. Toezien op de kwaliteit en project progress waren een uitdaging maar uiteindelijk bleek het een zeer geslaagde missie met een tevreden klant.
Heavy lifting Industry
Overhaul Offshore Mast Crane
Opdrachtgever Huisman Equipment B.V.
Site Coördinator
Om het Service team ter plaatse en de projectmanager in Nederland te ontlasten ben ik voor een aantal weken afgereisd naar Veracruz Mexico. Ter plaatse het contact met de klant hersteld en dagelijks de voortgang besproken, ervoor gezorgd dat benodigde materialen lokaal of vanuit Nederland aangeleverd werden en het Service team ondersteund waar mogelijk.
3D Design en 3D Printing
Industrieële componenten
VRM Services B.V.
Ontwerp en fabricage van industrieële componenten
Tijdens mijn projecten kom ik geregeld situaties tegen waarbij het design niet voldoet aan de gestelde eisen of esthetisch verbeterd kan worden. Zo had een klant bijvoorbeeld honderden meters noodstop trekkoord geïnstalleerd waar het koord door stalen beugels werd geleid. De doorvoergaten in deze beugels beschadigden het trekkoord. Hiervoor heb ik een slimme kunststof insert ontworpen welke zonder het koord te verwijderen in de beugel geplaatst kan worden. Inmiddels mocht ik meer dan 12.000 van deze inserts leveren.
Wat klanten zeggen
Peter is one of the most professional service engineers I have worked with. Besides his strong technical knowledge, he is a good communicator and sparring partner on all levels within the organisation. Peter is one of the few service engineers who is able to change his role as the situation on location occur (sales, diplomatic, trainee, r&d development). Furthermore he played an important roll into the development of commercializing after sales service. His personal characteristics makes him also a nice person to work with (calm, good sense of humour, serious if needed, customer focussed, keeps the companies interest in mind, comes with good ideas).
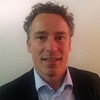
Boris van der Mee
I have been working with Peter for more than 18 months now and have hired him multiple times for specialist jobs on the Alfa Laval /Smit Gas Inert Gas Systems both in off-shore and marine applications. Peter has proven to be a true professional in all aspect of customer contacts and relations, technical matters. In addition Peter has a good eye for commercial opportunities and advises both customers and principals accordingly. Peter has proven to be reliable and trustworthy, a man of his word.
I can highly recommend Peter!
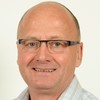
Mart Blankert
I highly reccomend Peter to every organization as a technical supervisor, site manager and system engineer.
He is very well educated and has a lot experience with handeling big building sites and systems in a industrial environment. Is technicaly completly up to date. He can manage large groups of subcontractors and has a excellent overview of all the projects.
Peter as a person is honest, straight forward and fun to work with.
He gets everyting done.
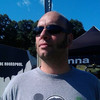
Rob Dekkers
We hired Peter on project base for a project in India. His effort to keep going forward definitely had his positive effect in a later stage of the project. Also his reports about problems and missing parts on site helped us to finish the project and end up with happy customer at the end.
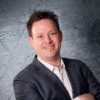
Tjerk Emmen
